Engineering Excellence
From Concept to Completion
Explore our end-to-end capabilities designed to deliver precision, reliability, and innovation.
Design & Prototyping
From concept to creation, our in-house design team and advanced prototyping capabilities help bring your ideas to life efficiently.
CAD/CAM Software
IM Gears uses CATIA and NX software as critical tools in its design and manufacturing concepts. We handle:
- Product Design
- Simulation and Analysis
- Prototyping
- Data Management
3D Printing for Rapid Prototyping
- Accelerated Development: Quickly transforms designs into physical prototypes, reducing lead time.
- Complex Geometry: Easily produces intricate shapes and designs that are challenging with traditional methods.
- Design Validation: Allows engineers to test form, fit, and function before full-scale production.
- Material Versatility: Utilizes diverse materials to mimic end-use product properties.
Dedicated Design and Prototype Assembly Cell
IM Gears’ dedicated design and prototype assembly cell ensures seamless integration of innovative designs with functional prototypes. Equipped with advanced CAD/CAM tools like CATIA and NX, and rapid prototyping capabilities, the cell supports swift iterations and validation. This enables the creation of assembly-ready prototypes tailored to customer specifications, streamlining the transition from concept to production.
Forging
Producing high-quality forgings for strength and precision, tailored to your specifications.
Cold Forming Process
IM Gears’ dedicated design and prototype assembly cell ensures seamless integration of innovative designs with functional prototypes. Equipped with advanced CAD/CAM tools like CATIA and NX, and rapid prototyping capabilities, the cell supports swift iterations and validation. This enables the creation of assembly-ready prototypes tailored to customer specifications, streamlining the transition from concept to production.
Warm Forging Units
Our advanced warm forging units bridge the gap between hot and cold forging, delivering superior mechanical properties with enhanced precision. This process minimizes material waste, reduces energy consumption, and produces components with excellent surface finishes and dimensional accuracy. With state-of-the-art equipment and expertise, we specialize in creating high-strength gears and shafts for demanding applications across automotive, aerospace, and industrial sectors.
Precision Machining
State-of-the-art CNC machining ensures tight tolerances and superior surface finishes.
CNC Turning
- Diameter 5mm to 250mm
- Length up to 1000mm
CNC Milling
- 3-Axis
- 4-Axis, and
- 5-Axis Machining Centers
Turn-Mill Machines with Live Tooling
Turn-mill machines with live tooling combine turning and milling operations into a single setup, enhancing efficiency and precision. At IM Gears, these advanced machines handle complex geometries with reduced cycle times, enabling seamless production of components with high accuracy. With 4-axis capabilities and live tooling, we deliver exceptional results for intricate parts across automotive, aerospace, and industrial applications.
Gear Processes
World-class gear manufacturing capabilities to meet diverse industry needs.
Gear Grinding
Gear grinding ensures the highest precision in gear profiles and surface finishes. At IM Gears, we utilize advanced Reishauer grinding machines to achieve exceptional accuracy, durability, and quiet operation. This process supports critical applications in automotive, aerospace, and industrial sectors, meeting the most demanding quality standards.
Skiving
We utilize advanced DVS Prawema technology to deliver gears with tight tolerances, exceptional surface finishes, and shorter lead times. Ideal for complex geometries, skiving supports demanding applications across automotive, aerospace, and industrial sectors.
Gear Honing and Shaping
IM Gears employs cutting-edge Nidec machines for gear honing and shaping, delivering superior surface finishes and enhanced gear performance. This process ensures precise geometry, reduced noise, and improved durability, making it ideal for automotive and aerospace applications where reliability is critical.
Heat Treatment & Special Processes
Enhanced durability and performance with precise heat treatment and specialized processes.
In-House Equipment
- ECM Vacuum Hardening
- Sealed Quench Furnace with Carburizing
- Magnetic Particle Inspection Units
Outsourced Processes
- Anodizing
- Cadmium Plating
- Passivation
Assembly & Testing
Integrated solutions for assembly and rigorous testing to ensure peak performance.
Capabilities
- Precision Assemblies for Gearboxes and Differentials
- Automated Vision Testing Systems
- Endurance and Functional Testing
Quality Systems: Metrology & Metallurgy
Uncompromised quality assurance through advanced inspection and testing capabilities.
In-House Equipment
- Gear Inspection: Klingenberg P40, Wenzel Gear Measurement Machines
- CMM: Zeiss and Renishaw Systems
- Metallurgical Lab: Hardness Testers, Microstructure Analysis
Digital – Industry 4.0
Leveraging digital solutions to optimize efficiency and transparency.
Capabilities
- IIoT-Enabled Machines for Real-Time Monitoring
- Digital Twin Technology
- Smart Manufacturing Analytics
Our Capabilities
CAD/CAM Software
IM Gears uses CATIA and NX software as critical tools in its design and manufacturing concepts. We handle:
- Product Design
- Simulation and Analysis
- Prototyping
- Data Management
3D Printing for Rapid Prototyping
- Accelerated Development: Quickly transforms designs into physical prototypes, reducing lead time.
- Complex Geometry: Easily produces intricate shapes and designs that are challenging with traditional methods.
- Design Validation: Allows engineers to test form, fit, and function before full-scale production.
- Material Versatility: Utilizes diverse materials to mimic end-use product properties.
Dedicated Design and Prototype Assembly Cell
IM Gears’ dedicated design and prototype assembly cell ensures seamless integration of innovative designs with functional prototypes. Equipped with advanced CAD/CAM tools like CATIA and NX, and rapid prototyping capabilities, the cell supports swift iterations and validation. This enables the creation of assembly-ready prototypes tailored to customer specifications, streamlining the transition from concept to production.
Cold Forming Process
IM Gears’ dedicated design and prototype assembly cell ensures seamless integration of innovative designs with functional prototypes. Equipped with advanced CAD/CAM tools like CATIA and NX, and rapid prototyping capabilities, the cell supports swift iterations and validation. This enables the creation of assembly-ready prototypes tailored to customer specifications, streamlining the transition from concept to production.
Warm Forging Units
Our advanced warm forging units bridge the gap between hot and cold forging, delivering superior mechanical properties with enhanced precision. This process minimizes material waste, reduces energy consumption, and produces components with excellent surface finishes and dimensional accuracy. With state-of-the-art equipment and expertise, we specialize in creating high-strength gears and shafts for demanding applications across automotive, aerospace, and industrial sectors.
CNC Turning
- Diameter 5mm to 250mm
- Length up to 1000mm
CNC Milling
- 3-Axis
- 4-Axis, and
- 5-Axis Machining Centers
Turn-Mill Machines with Live Tooling
Turn-mill machines with live tooling combine turning and milling operations into a single setup, enhancing efficiency and precision. At IM Gears, these advanced machines handle complex geometries with reduced cycle times, enabling seamless production of components with high accuracy. With 4-axis capabilities and live tooling, we deliver exceptional results for intricate parts across automotive, aerospace, and industrial applications.
Gear Grinding
Gear grinding ensures the highest precision in gear profiles and surface finishes. At IM Gears, we utilize advanced Reishauer grinding machines to achieve exceptional accuracy, durability, and quiet operation. This process supports critical applications in automotive, aerospace, and industrial sectors, meeting the most demanding quality standards.
Skiving
We utilize advanced DVS Prawema technology to deliver gears with tight tolerances, exceptional surface finishes, and shorter lead times. Ideal for complex geometries, skiving supports demanding applications across automotive, aerospace, and industrial sectors.
Gear Honing and Shaping
IM Gears employs cutting-edge Nidec machines for gear honing and shaping, delivering superior surface finishes and enhanced gear performance. This process ensures precise geometry, reduced noise, and improved durability, making it ideal for automotive and aerospace applications where reliability is critical.
Heat Treatment & Special Processes
In-House Equipment
ECM Vacuum Hardening
Sealed Quench Furnace with Carburizing
Magnetic Particle Inspection Units
Outsourced Processes
Anodizing
Cadmium Plating
Passivation
Assembly & Testing
- Precision Assemblies for Gearboxes and Differentials
- Automated Vision Testing Systems
- Endurance and Functional Testing
Quality Systems: Metrology & Metallurgy
- Gear Inspection: Klingenberg P40, Wenzel Gear Measurement Machines
- CMM: Zeiss and Renishaw Systems
- Metallurgical Lab: Hardness Testers, Microstructure Analysis
Digital - Industry 4.0
- IIoT-Enabled Machines for Real-Time Monitoring
- Digital Twin Technology
- Smart Manufacturing Analytics
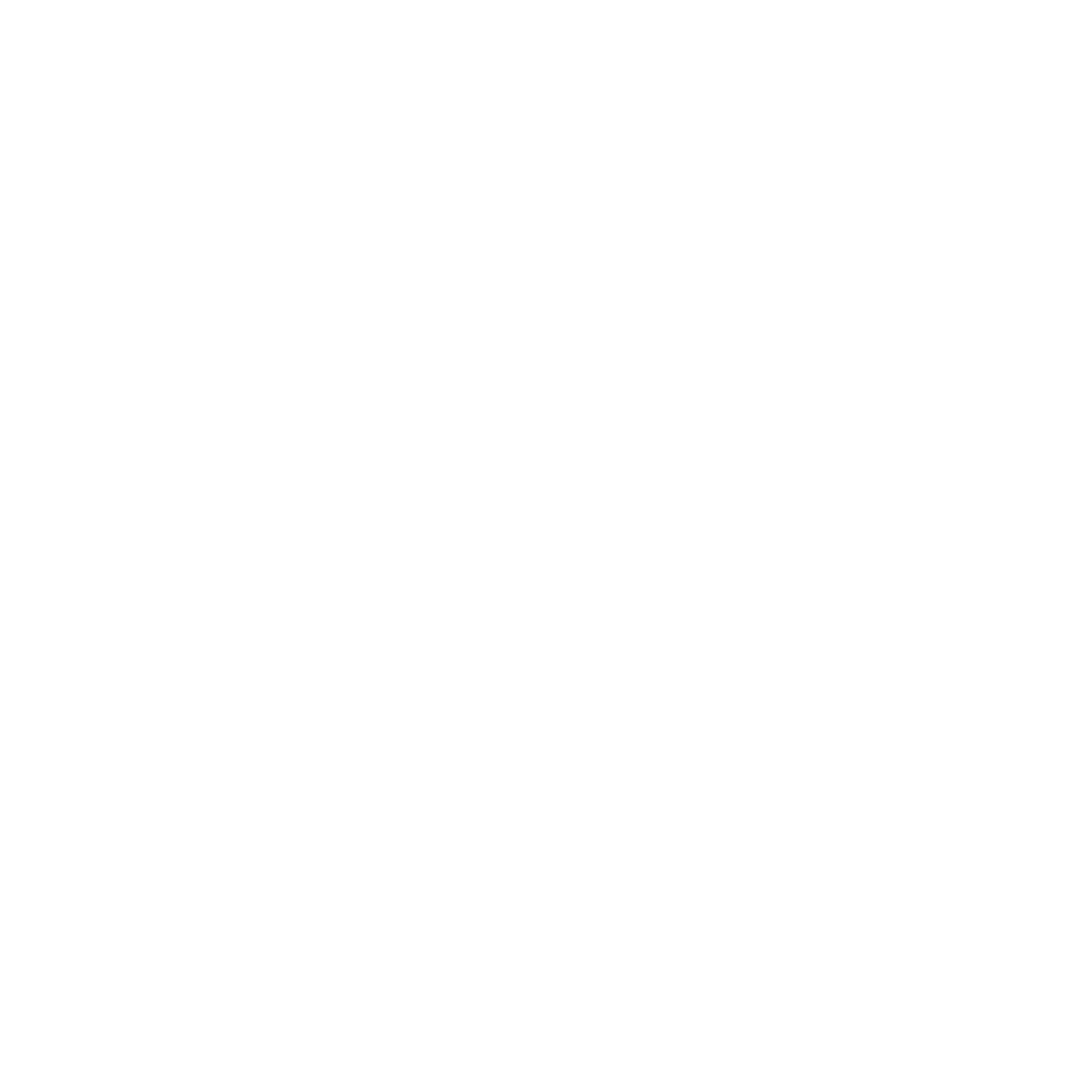
I M GEARS PRIVATE LIMITED
235 1A & 2C Vengaivasal Main Road
Madambakkam post, Selaiyur
Chennai - 600 073
Tel : +91 44 2278 0085 / +91 98410 92730
email: marketing@imgearsindia.com
Investor Relations
Get in Touch
Have questions? Reach out to us today.